Blog
4 ways to optimize material transport
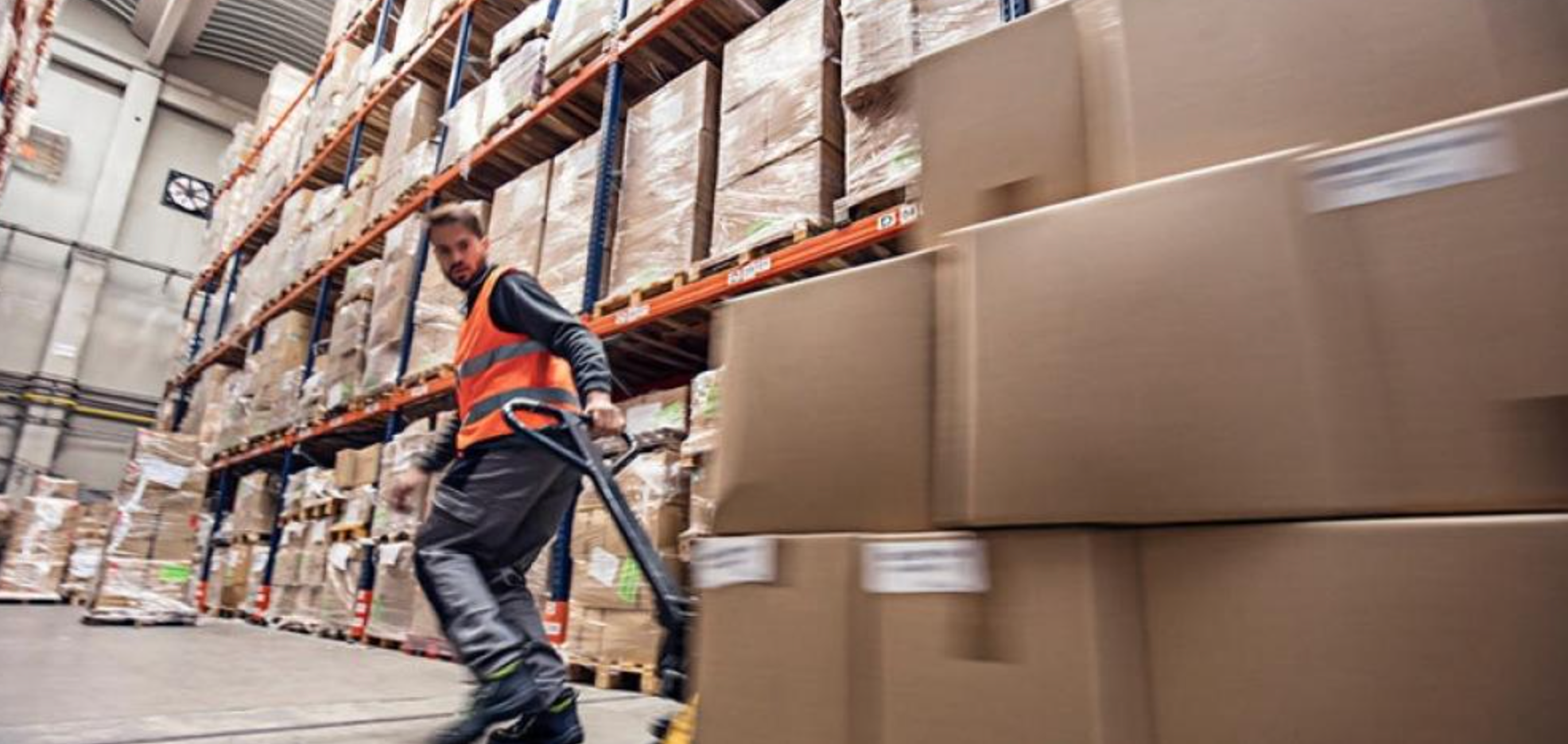
Material transport can be perceived as the "first mile" - the manufacturer's equivalent to the last mile concept in delivering products or goods to a customer. The first mile draws parallels to the last mile; they share many of the same challenges, yet the last mile seems to continually be the focus of attention when looking to improve delivery time and costs in the supply chain. Arguably, manufacturers are spending too much time trying to save costs in the last mile without considering opportunities to optimize material transport within the first mile, especially indoors. Here are four steps that can be taken today to poise your operation for the future:
1. Find the right technology
Evolving technologies provide a new paradigm for the often overlooked material transport link in supply chain. The market for Industrial robotics, for example, is expected to reach to $79.6 billion (USD) by 2022. Sensors are becoming more accessible, more advanced, and available at a better price. When integrated with robotic systems spanning automated picking in order fulfillment to autonomous material transport, sensors can help to provide accuracy, efficiency and insight into traceable KPIs.
Meanwhile, the user interface of the software is designed to integrate with inventory management or work order tracking systems, and can interconnect with equipment on the floor.
2. Adopt operational processes that optimize throughput
With an evolving marketplace, factory operations cannot operate today like they did a decade ago - change must happen in order to survive. This may come in the form of outsourcing strategic business units or revitalizing existing policies. Internal policies can become habitual and neglected. 5S, for instance, is a tried and true systematic and methodical approach allowing teams to organize the workplace in the safest and most efficient manner. Often overlooked in day-to-day operations, a typical 5S implementation can result in significant reductions in the square footage of space needed for existing operations. It can also be extended to material transport to ensure materials are optimally dispatched and transport methods, whether manual or automated, can reach the destination without stoppages or limitations.
3. Move less inventory, just-in-time
Material that flows in a facility, and the operational methods of that material transport including its packaging, are designed around the traditional material handling paradigm - people. If operations strive to attain lean manufacturing and integrate autonomous material flow methods, then why do they allow suppliers to ship oversized, bulk pallets in arrangements that are convenient for them and not necessarily the manufacturer? Operators can embrace conversation with suppliers to change the way materials are packaged and delivered, and, in turn, move inventory faster throughout the plant to deliver to the designated station at the right time and in the right quantity; thus eliminating wasted space and motion.
4. Design the layout for optimized efficiency and scalability
The layout that is currently in place may not be the most optimized for material transport. Recognize how goods are currently received and how they should be received to enable faster dispatch in your operation. Also understand the nature of inventory orders (size, storage, and packaging), transportation modes needed for goods, and skills and training required by employees. Then, identify business process requirements and technologies that can be implemented. This introspective approach may call for a floor plan redesign, particularly if material transport equipment can move shrunken inventory through smaller spaces to deliver on a more direct route.