Blog
Inefficient material handling leads to supply chain problems
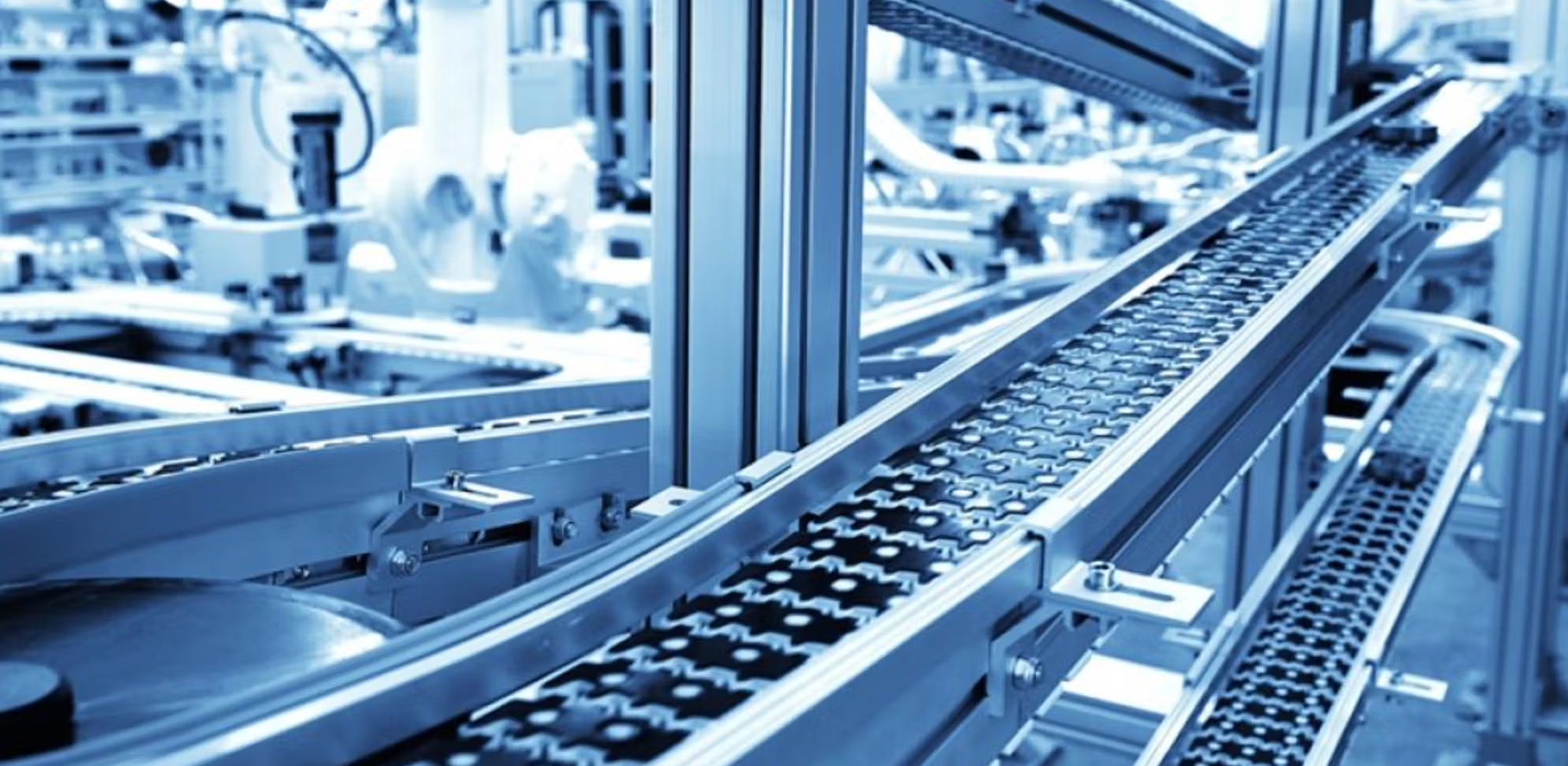
Every manufacturer is challenged by how to best handle the materials that go into their production. Even an automated production system can have areas of inefficiency which affect many other parts of the manufacturing process, leading to product loss, wasted time, and increased costs.
A primary goal of materials handling is efficiency and ultimately to reduce production costs and other supply chain problems. And clearly, improper materials handling will result in a higher manufacturing cost per unit. The good news is improving material handling through techniques like production levelling extend beyond the immediate benefit of helping manufacturing run more smoothly. When materials move efficiently through a manufacturing process, all the related supply chain functions can remain focused on their core responsibilities.
Production levelling
One technique of product levelling to help with materials management is known as heijunka, a part of Lean. The intended effect is to level demand and flexibility by averaging production volume over the long-term. Its overall objective is to match production with customer demand while using production resources optimally. Lead times and production are better predicted and faster because of the even planning process. Without a production levelling process, any variation in demand will affect materials management leading to inefficiencies for other connected supply chain functions like shipping and receiving.
Systems-based materials storage
How and where materials are stored is vital to their efficient use as well. Some manufacturing facilities use manual, labor-intensive processes for storing materials. An example could be the use of separate maintenance parts storage areas, located in remote locations in the plants. This results in a slower access to parts service parts that are far away from the production line. The problem is more than just extra time for retrieval. The important point is that long material transport does not add any value to the operation and can also affection the condition of the materials. Moving to a systems-based storage process improves material handling leading to a more efficient operation.
Inventory tracking
The importance of accurate inventory counts is self-evident, as is the ability to quickly locate specific items. Without a plan for tracking material inventory and parts, finding them becomes impossible. If a plant does not track materials and parts by user, task, and location - through a system like RFID - reporting usage becomes difficult and inventory counts will be off. With proper visibility to material and parts, the rest of the organization can plan against level production of these parts.
From the moment parts and raw materials enter the manufacturing facility through to the finished product, materials are handled multiple ways and under different circumstances. This movement of goods is an integral part of the manufacturing process so if it is not operating efficiently at any point, there consequences for production and other business functions - like the supply chain should always be considered.